HOME PRODUCTS LAB DIVISION
The FVA/A1 Vertical Lab Sterilizer combines design with Excellent performances and simplicity of use.
The automatic vertical sterilizer FVA/A1 has been specifically designed and developed to meet the most demanding application requirements in many different sectors, from universities to quality control laboratories in pharma, food or cosmetics industrial sectors.
FVA/A1 autoclave is the perfect solution for highly specialized fields and challenging customers worldwide that demand exclusive, reproducible and validated processes. These sterilizers have been designed with ergonomical features for easy handling and daily use.
The basic version of FVA/A1 can be used for standard processes and is easy to configure, thanks to its conceptual design and modular construction with exclusive optional kits. Please, click on the link “recommended kit” to check out all possible configurations referred to FVA/A1 series.
DESIGN & TECHNICAL FEATURES
FVA/A1 autoclaves are available with three different chamber volumes: 75 liters (FVA2/A1), 140 liters (FVA3/A1) and 188 liters (FVA3/A1 Plus).
FVA/A1 lab sterilizers are equipped with 316L stainless steel chamber and lid with automatic independent operation and control. The access to the technical area is assured by a wide front door with a special safety lock for easy maintenance.
The exclusive horizontal swivelling lid has a patented seal with compressed air system for perfect airtight, safety and easy maintenance.
An internal heat exchanger, made of 316L stainless steel and a fan for rapid cooling system can be integrated in the lid. An internal heat exchanger, made of 316L stainless steel and a fan for rapid cooling system can be integrated in the lid. The DCS20 process controller allows fully programmability: 30 cycles easy to customize in a multi-user environment and an interface for remote monitoring via Ethernet protocol.
The DCS20 process controller allows fully programmability: 30 cycles easy to customize in a multi-user environment and an interface for remote monitoring via Ethernet protocol. The operating software is fully validated and documented.
KEY BENEFITS
- Satisfies the most rigid requirements of safety and quality according to international standards.
- New materials providing chemical inert insulation and both thermal and acoustic: smoother, quieter and safer operations.
- Energy saving system.
- Functional and attractive design.
- High level of programming and control versatility.
- Innovative and unique modular design.
- Ideal positioning of operator panel and printer.
- Optimized loading height from floor.
- GLP compliance
COMPLIANCE TO
- PED Directive 2014/68/UE – Pressure equipment
- Machine Directive Macchine 2006/42/EC
- EMC Directive 2014/35/UE
- LVD Directive 2006/95/UE
Want to know more about our certifications? Please visit the dedicated section or do not hesitate to contact us.
STANDARD
- EN ISO 12100 Safety of machinery – General principles for design – Risk assessment and risk reduction
- EN ISO 13857 Safety of machinery – Safety distances to prevent hazard zones being reached by upper and lower limbs
- EN ISO 13849-1 Safety of machinery – Safety-related parts of control systems – Part 1: General principles for design
- EN IEC 60204-1 Safety of machinery – Electrical equipment of machines – Part 1: General requirements
- EN IEC 61326-1 Electrical equipment for measurement, control and laboratory use – EMC requirements – Part 1: General requirements
- EN 61010-1 Safety requirements for electrical equipment for measurement, control, and laboratory use – Part 1: General requirements
- EN 61010-2-040 Safety requirements for electrical equipment for measurement, control, and laboratory use – Part 2-040 Particular requirements for sterilizers and washer-disinfectors used to treat medical materials
- EN 13445-3 Unfired pressure vessels – Part 3: Design
- EN 4126-1 Safety devices for protection against excessive pressure – Part 1: Safety valves
STANDARD COMPLIANCE FOR NON-EU COUNTRIES
United States of America (USA)
- ASME (American Society of Mechanical Engineers) U & S Stamp
- UL 508 A Standard for Industrial Control Equipment
- NPFA 70 National Electrical Code (NEC
- NPFA 79 Electrical Standard for Industrial Machinery
People’s Republic of China
- SELO – Chinese Safety Regulation for Pressure Vessel
Russian Federation
- TR CU 032 On the safety of equipment operating under excessive pressure
- TR CU 010 Machinery Directive
Brazil
- NR 13 Boilers and Pressure Vessel
Malaysia
- Department of Occupational Safety and Health (DOSH)
Singapore
- Ministry of Manpower (MOM)
DOWNLOAD
Catalog
FVA Vertical Lab Sterilizer
White papers
Moist-heat sterilization – Highlights on equivalent time F0
RELATED PRODUCTS
Can we help you?
DCS20
The DCS20 process controller was specially designed for laboratory machines manufactured by Fedegari.
The end result is a modular system that offers a wide range of functions and high reliability.
The system includes a supervisor module and other individual ones dedicated to specific functions such as: programs management, cycles, phases, configurations and alarms for the module.
Options
- REMOTE GUI allows remote connection to a PC by Ethernet connection. This connection allows the operator to view the machine display on the desktop.
- REMOTE CONTROL allows remote connection to a PC by the Ethernet connection port. This connection allows the operator to fully interact with the machine. This excludes door closing and data backup operations.
Data management in compliance with the requirements of the 21 CFR PART 11 protocol.
Life cycle and Validation
DCS20 is designed, developed, tested, maintained, and validated according to a defined life cycle according to regulatory requirements stated in the current GMP.
Life cycle management complies with FDA 21 CFR Part 11, up to the current operational stage in defining product management practices in accordance with the principles of the GAMP5 guideline.
According to the system classification defined in GAMP 5 – Appendix M4 Categories of Software and Hardware, DCS20 is classified as:
- Software Category 4 – Configurable system
- Hardware Category 1 – Standard hardware components
Tests on software and hardware components are performed, during project and engineering activities, by applying functional risk analysis according to ALCOA+ principles, as defined in the Change Control procedure, dedicated to DCS20, part of the Fedegari Quality System.
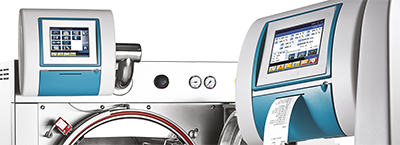